Exploring the Role of Semi Automatic hydraulic shearing machine in Modern Industry
Users in various industries depend on semi-automatic hydraulic shearing machines to perform accurate sheet metal cuts through hydraulic power systems. Producers obtain precise effective reliable cuts through the combination of semi-automation techniques and hydraulic power. The popularity of this shearing machine increased because it successfully deals with challenging cutting tasks by achieving a blend of automated and manual operation. The semi-automatic hydraulic shearing machine has become popular within the market by offering dependable performance to operators with both small workshops and industrial-level factories.
Understanding Semi Automatic hydraulic shearing machine
Semi-automatic hydraulic shearing machines use hydraulic power to drive their cutting blade for creating precise and clean metal cuts across steel or aluminium materials. The semi-automatic design results in manual material feeding operations but the machine performs automatic cuts independently. The manual and automated system integration grants operators complete operational control while guaranteeing high quality results. Thicker and stronger materials become feasible for hydraulic shearing machines compared to mechanical and pneumatic methods because they produce cutting power from hydraulic cylinders. The blade shows flexibility because workers can easily modify both its cutting gap and angular position to accommodate diverse materials and thickness levels.
Key Features of Semi Automatic hydraulic shearing machine
- The basic structure of these devices rests on hydraulic power because their hydraulic system enables them to create powerful cutting force effortlessly. The precise and consistent cutting of thicker materials becomes possible despite the feature.
- Humans can operate the feeding steps while changing parameters by hand but the automated cutting system runs independently. The operator gains independence and complete command over their operations through this feature.
- A hydraulic shearing machine enables users to modify the blade gap settings through its adjustable feature which stands as its essential key characteristic. A hydraulic shearing machine needs this feature because it ensures accurate cuts particularly for materials that differ in thickness.
- The intense forces produced throughout shearing operations require such equipment to use a substantial sturdy frame as its base. Testing conditions are no match for this strong frame structure which ensures the machine performs reliably over time.
- Semi-automatic hydraulic shearing machines incorporate safety components between features that include safety guards and emergency stop systems for accident prevention and secure workspaces.
- Numerous machines are equipped with a back gauge system that lets users measure and position sheet metal before cutting. Such features provide precise and uniform cutting abilities while enhancing production effectiveness in various work areas.
- User comfort and labor fatigue decrease through foot pedal operation since operators can use their feet to activate the cutting mechanism.
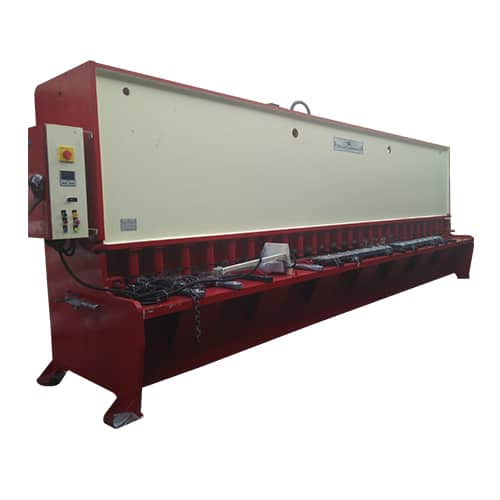
The Role of Semi Automatic hydraulic shearing machine Manufacturers
Production facilities heavily depend on semi-automatic hydraulic shearing machines because sheet metal cutting occurs frequently within their sectors. Semi-automatic hydraulic shearing machines remain essential to produce vehicle, building and ship components. Such equipment remains necessary when precision and speed requirements exist because they manage materials efficiently while maintaining precise control. Production efficiency increases in workshops of all sizes with reduced manual labour as well as improved productivity through semi-automatic shearing machines.
Together with preventing user injuries, these devices operate to reduce production expenditures. The machines provide extended economic advantages through high material processing capacity alongside minimal operational stoppages, although requiring an initial capital expenditure. The semi-automatic functionality gives operators process control of pivotal aspects like material alignment along with preserving automated system speed and precision.
Applications of Semi Automatic Hydraulic Shearing Machines
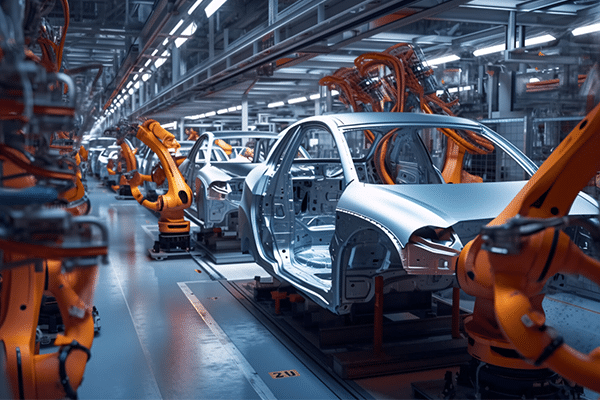
Vehicle Industry
Sheet metal manufacturers use these machinery to cut their materials before forming them into vehicle components such as body panels and chassis parts as well as structural elements. Machine accuracy stands as an essential factor because it enables precise automotive production measurements to be preserved.
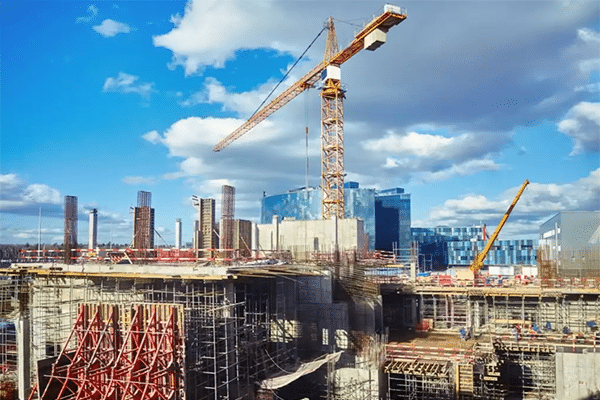
Construction Industry
Modern building and infrastructure require cut metal sheets for roofing and structural components and frameworks which semi-automatic hydraulic shearing systems operate on. The equipment functions optimally with heavy-gauge metals to produce long-lasting building elements.
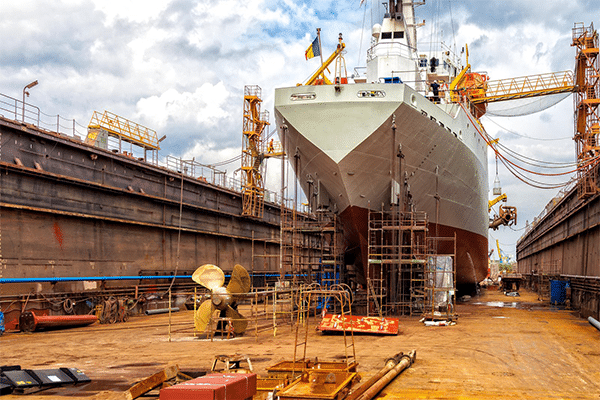
Shipbuilding
Harsh environmental conditions require shipbuilding operations to use materials which withstand such conditions effectively. Mechanical shear machines process thick steel and aluminium materials to produce different ship components for both hulls and superstructures. For safety and performance compliance ships need accurate cutting of large material sections.
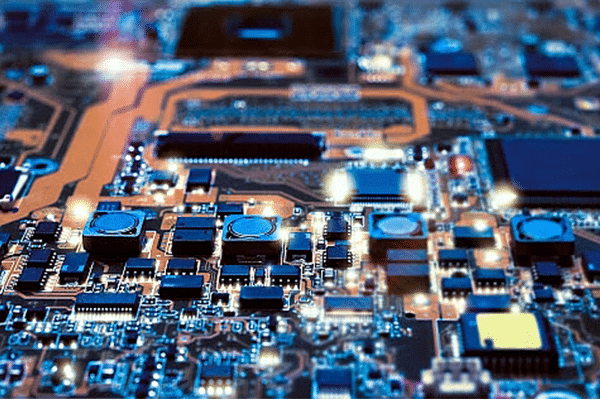
Electronics Industry
The exact cuts of copper and aluminium materials through this industry enable producers to create heat sinks and control panels in addition to electrical enclosures. The semi-automatic hydraulic shearing machine ensures necessary precision during delicate operations.
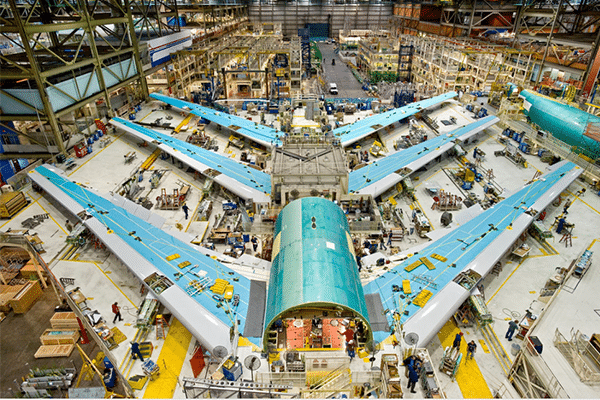
Aerospace Industry
In aerospace applications one needs high-performance materials to produce exact components. Cuts of titanium and composite metals happen through semi-automatic hydraulic shearing machines to produce aviation parts.
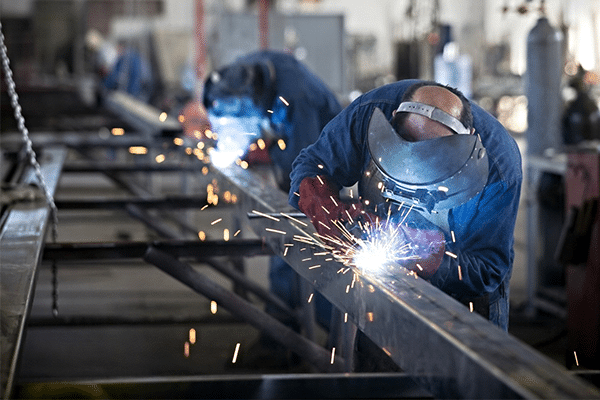
Metal Fabrication
General metal fabrication companies use these machines to make precise metal cuts of various materials which form specific customer orders. Workshops choose these machines first since they generate exact cuts while using limited material resources in situations requiring high efficiency and material management.
Future Trends in Semi Automatic Hydraulic Shearing Machines
The future of hydraulic press machine manufacturing is marked by continued innovation and technological advancements. Key trends shaping the industry include:
-
The manufacturing industry of hydraulic press machines contains a future direction focused on technology development coupled with ongoing innovations. Several prominent industry trends currently lead the semi-automatic hydraulic shearing machine industry forward.
-
Robotics and artificial intelligence, together with automation technologies, are transforming hydraulic press machine processes by building integration systems. Manufacturing becomes more efficient through automatic systems which simultaneously decrease human mistakes and create ease of integration between manufacturing processes.
-
Production facilities enhance their hydraulic press machines by installing smart functionality through Industrial 4.0 protocols which incorporate IoT-enabled devices and data processing systems.
-
The rise of sustainability has led hydraulic press machine manufacturers to develop sustainable products because it is now a critical requirement. The manufacturing approach focuses on energy-efficient design principles together with materials that are recyclable and green manufacturing procedures.
Advanced hydraulic press machines continue developing to suit the production requirements of new high-strength alloys and composites. Manufacturers stay active in creation through their nonstop advancement to handle modern material technology needs..